What is a hybrid rocket?
A hybrid rocket is a rocket engine system consisting of two different types of propellants, mainly solid fuel and liquid oxidizer, which are burned to produce thrust. Since the fuel and oxidizer do not mix spontaneously, there is no risk of explosion.
There are three mains advantages of hybrid rockets.
- High safety and low cost : Easy handling and management due to low explosion hazard
- High functionality in combustion control : easy combustion interruption and re-ignition, and thrust control by simply changing the amount of oxidizer supplied.
- Simple system: the only liquid is the oxidizer, and the structure is not as complex as a liquid rocket.
Conversely, there are three disadvantages of hybrid rockets
- Low combustion efficiency
- Low combustion regression rate
- Change in fuel/oxidizer mixing ratio (O/F)
A-SOFT (Alternating Swirl Oxidizer Flow Type) hybrid rocket
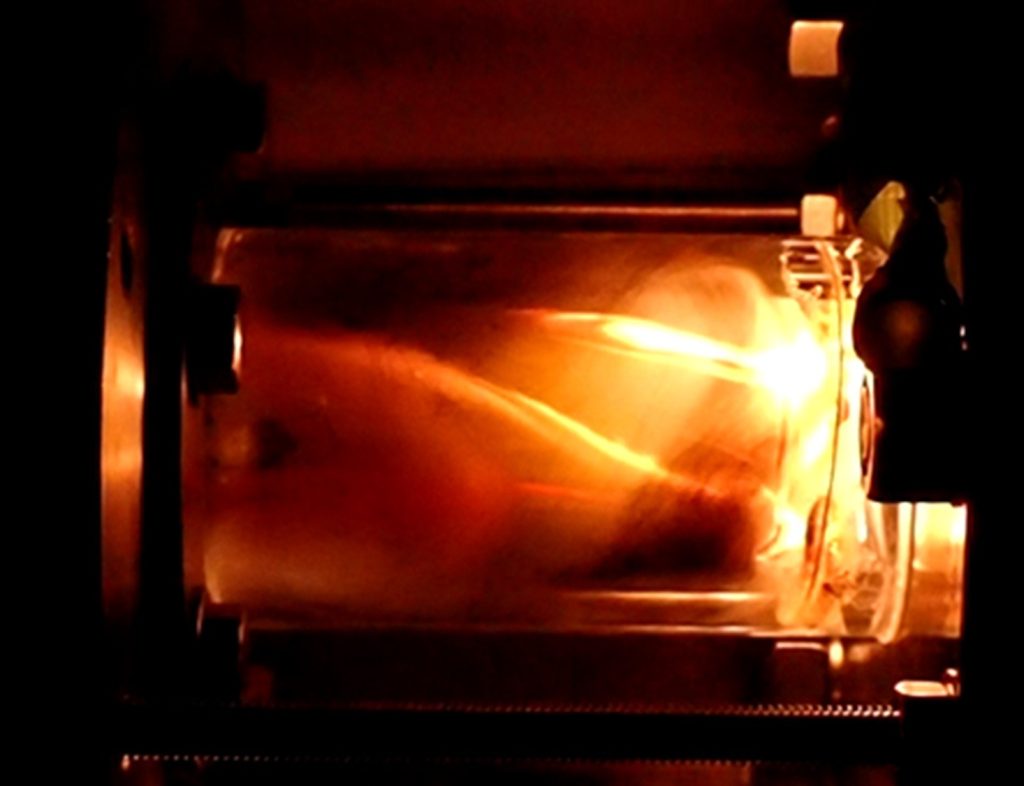
Photo Combustion of A-SOFT
A-SOFT is a system that solves the above shortcomings of hybrid rockets by providing two types of injectors, one for swirl flow and the other for axial flow, and independently controlling the flow rate.
The oxidizer is sprayed in a swirling stream, bringing the flame surface closer to the solid fuel and increasing the fuel recession velocity. Independent control of the two flow rates enables simultaneous control of the fuel/oxidizer mixing ratio (O/F) and thrust.
Basic research on A-SOFT hybrid rocket
[Experimental measurement of heat transfer characteristics of liquid oxygen]
A-SOFT requires the use of a gaseous oxidizer rather than a liquid one to inject a swirling flow of high intensity. A regenerative-cooling nozzle was devised to vaporize the oxidizer while the liquid oxidizer flows over the nozzle wall and cools the nozzle. In order to design this nozzle, we are conducting research to measure the heat transfer characteristics of the rocket nozzle under ambient conditions.
[Research and Developing of Hybrid Rocket Thrust Control System]
A hybrid rocket engine (HRE) is said to be the future of the rocket propulsion system as there are many advantages over liquid and solid fuel rocket engines, such as high safety, low cost, non-toxic propellant, and simplicity. With these advantages, many researchers and private aerospace companies attempt to develop HRE for payload launchers and human space launch vehicles.
However, nobody successfully develops an orbital-class rocket propelled by HRE because the combustion characteristic of HRE is still a challenge to predict and measure. During the burn, the fuel port will expand and causes the oxidizer to fuel mass ratio (O/F ratio) to shift from the optimum value. Moreover, it is challenging for the fuel mass measurement because the fuel is in a solid state, which too means that almost impossible to measure the O/F ratio directly during the burn. The impact is the reduction of the rocket efficiency and causes some residue fuel. Thus, it is critical to control the combustion process of the rocket during the flight.
Our research goal is to research and develop a thrust control system for an actual flight HRE to be as simple as possible with acceptable efficiency for the orbital flight. The research will allow HRE to comply with the orbital-class rocket in the future.
[the effect of the injected oxidizer temperature on fuel regression rate]
A hybrid rocket utilized A-SOFT technology, the injected oxidizer must be in gaseous state. In this case, a regenerative cooling nozzle can be used as liquid oxidizer vaporizer. When liquid oxidizer is subjected to phase change when it passes through the hot nozzle, the temperature of the gaseous oxidizer can go higher than normal injection temperature. This is possible when more heat is transferred to the vaporized oxidizer before it leaves the cooling channels. This increase in injected temperature is expected to affect the fuel regression rate of a hybrid rocket engine. This is an advantage for hybrid rocket engine that use thermoplastic as its fuel which is PMMA in our case. Therefore, in this research we aim to investigate the effect of the injected oxidizer temperature on fuel regression rate. The primary investigation was done by open combustion experiment of PMMA/GOX hybrid rocket engine. The experiment was carried out under the oxygen mass flow rate of 4 and 8 g/s with the temperature of normal GOX injection temperature, 75 and 120 degrees Celsius. From the result of this primary experiment, it is observed that the fuel regression rate does slightly increased as GOX temperature increased. Setup for next experiment with rocket nozzle attached to the rocket is under study and design to obtain the expected result of the combustion at elevated chamber pressure like those in actual rocket operation.